- 事例紹介
- IT活用
BEFORE & AFTER
- ・既存のWMS(倉庫管理システム)とオートラベリングシステムの連携で、仕分け作業が2.5時間に短縮
- ・残業を大幅に改善、週休2日(年間休日105日)を実現
- ・ラベルの貼り間違いがゼロに
- ・数字を使用することで未経験・外国籍スタッフでも仕分け作業がすぐに可能になり、ミャンマーから6名雇用。人手不足や熟練者の不在にも対応可能なシステムを構築
株式会社ホクガンは、冷凍倉庫業を主たる事業として1967年に設立されました。県内スーパーやコンビニエンスストア、病院などへの商品卸売・配送で沖縄の物流を支えるとともに、プライベートブランド商品の製造・販売も手がけ、スタッフは2023年8月現在パート・アルバイトを含め480名を数えます。
今回お話を伺ったのは、取締役常務 物流センター長の石原智(いしはらさとし)さん。仕分け作業にオートラベリングシステムを導入し、残業が多く、定着率も上がらなかった物流部門の業務を大きく変えた立役者です。
非効率的な作業で常態化する残業、定着しないスタッフ
2005年に入社し、営業、倉庫、人事を経て2011年から物流部署に配属された石原さん。社内システム部で開発したWMS(倉庫管理システム)が導入され「ある程度の自動化、効率化は図られていた」ものの、ケース商品の仕分け作業に課題と改善の必要があると感じたのだそうです。
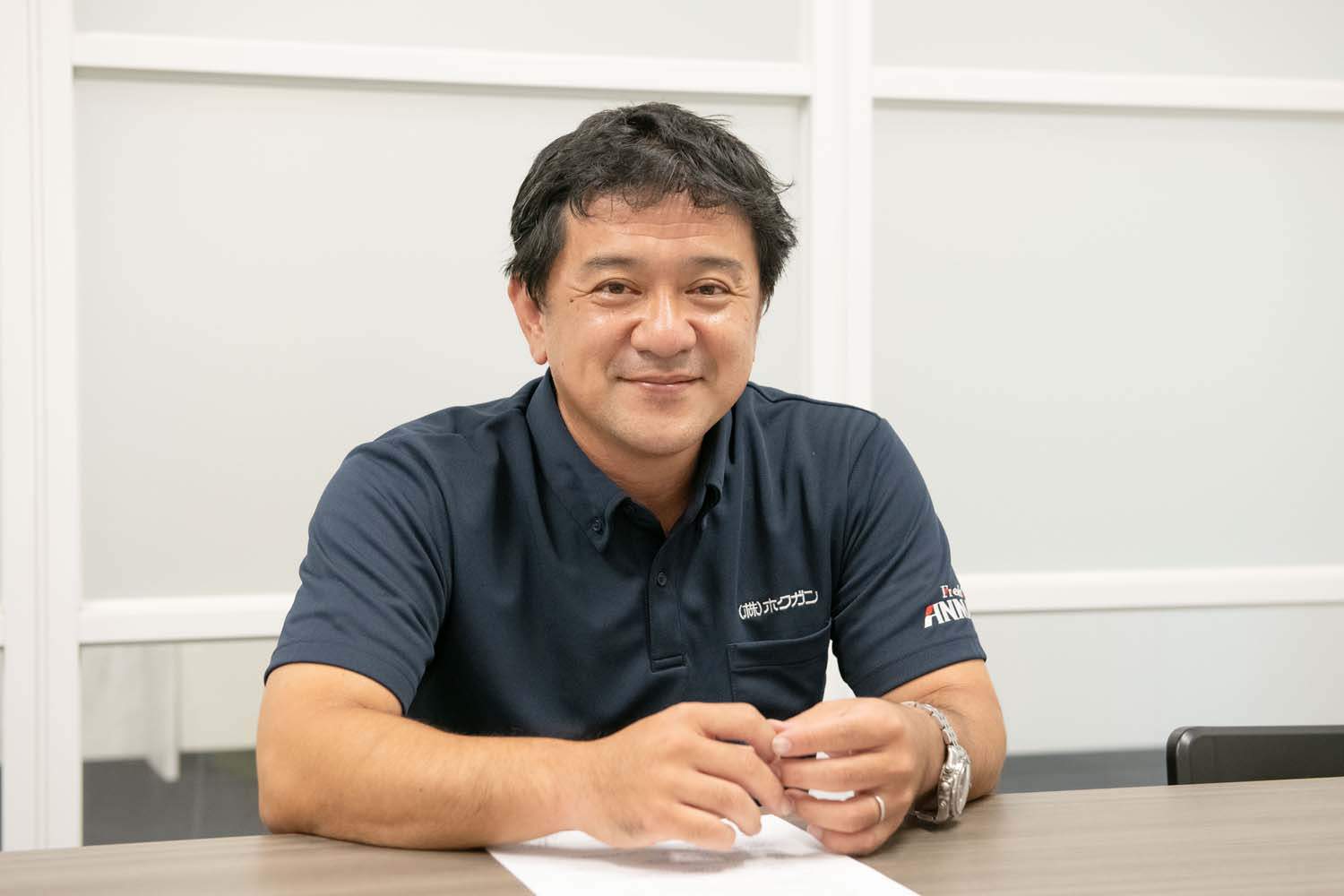
「ケース商品の仕分けは、パレットに積まれた商品の商品コードをハンディターミナル(バーコード読取機)で読み、数を確認してラベルを貼付、レーンの上を手動で転がしながら移動し、配送先ごとに台車に積み込むという手順。体力を使い時間がかかることはもちろん、類似商品やフレーバー違いの商品でラベルを貼り違えてしまうこともあり、そのヒューマンエラーは、1日10件以上発生していました」
決して効率が良いとは言えない作業手順で、1取引先につき60以上の店舗に、食品だけで約4000の商品を仕分けることも。貼り違えたラベルの修正、再チェックにも時間を取られ、残業は1日3~4時間が常態化していました。
経営陣もこうした状況を改善すべき課題ととらえ、残業時間削減の対策検討が始められます。新たな雇用も試みたそうですが、人材不足で応募は少数。採用できたとしても、残業の多さから1~2カ月で辞めてしまう場合も多く、職場環境改善の必要性が浮き彫りになりました。
実際に現場に入り、作業を事細かに観察し、改善点を把握していた石原さんは、「システム導入や自動化で業務を効率化し、職場環境を改善することが必要」と確信。東京で開催される物流関連システムの展示会への参加や県外物流企業の見学などを通し、日々の業務の中で洗い出していた仕分け作業の課題解決やニーズを実現できるシステムの導入へ動き始めます。
石原さん
「県外企業のシステムは大規模で先進的でしたが、そっくりそのまま持ってきても弊社の規模やフローに合いません。色々な企業のシステムややり方を参考にして、現在のオートラベリングシステム(※仕分けラベル貼付を自動化するシステム)に行きつきました」
現場ファーストのシステム導入で作業時間4時間→2.5時間
石原さんは、やりとりを通して思い描くシステム、レイアウトを一緒に作ってくれると感じたメーカーをパートナーに選定。WMSとの接続のため社内システム部と連携しつつ、約2年をかけて導入に至りました。
導入したシステムでは、レーンに流したケース商品の商品コード読込、オートラベラーでのラベル生成・貼付、バーコードリーダーによるチェックまでが自動で行われます。
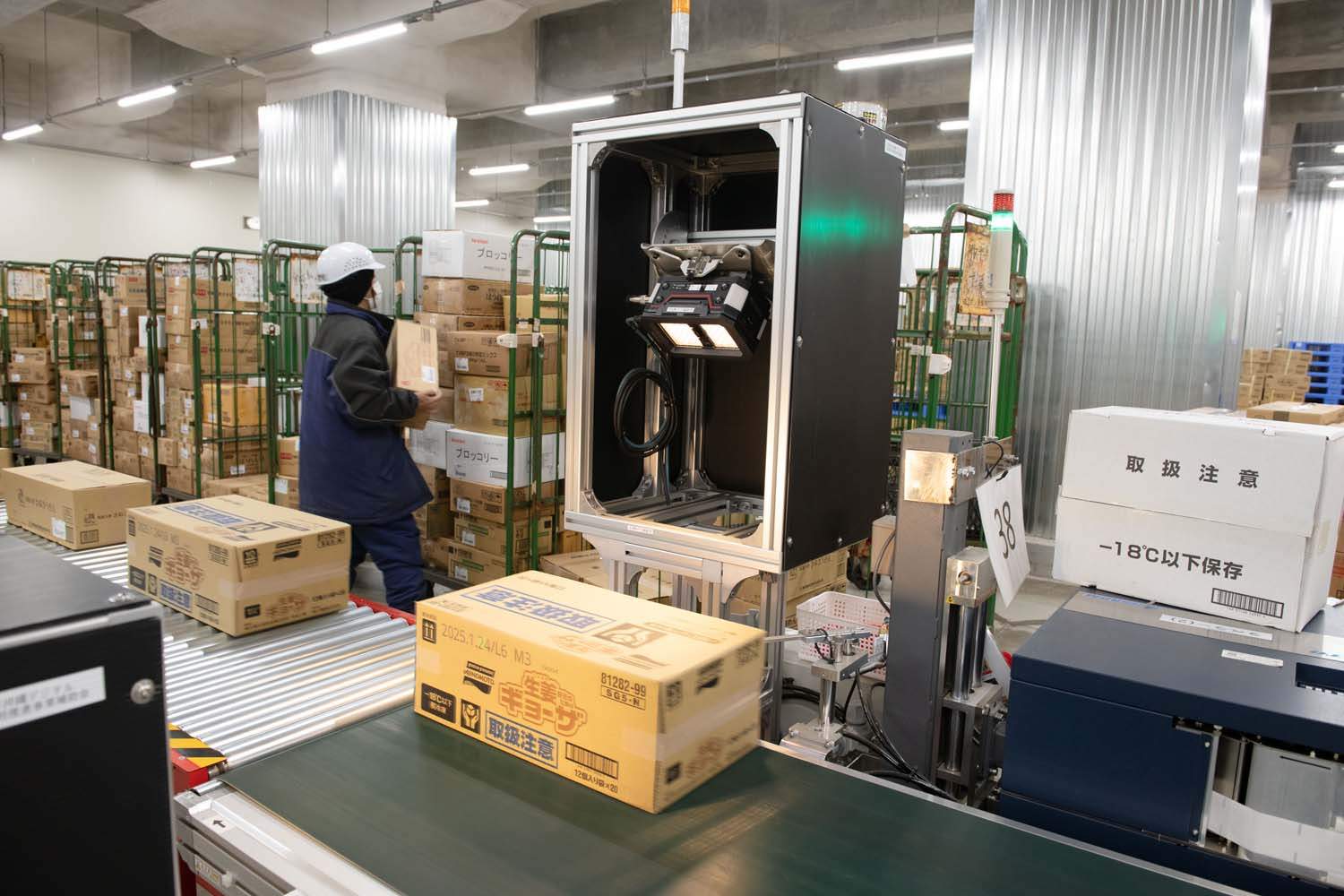
「倉庫内でいかに無駄なく効率的な導線を作るか、また、トラブルが起きた時のリカバリーをどうするか。高額の費用が必要なシステムでもあり、失敗は許されないと考え、何十回も図面を書き換えました。
例えば、2本のレーンの間のスペースとオートラベラーの2機配置。どちらかのレーンがエラーなどで使えなくなっても、もう一方のレーンから作業できるように、スペースを空けてレーン外側と内側にオートラベラーを配置してもらいました。スペースは、壊れやすくレーンに流せない商品を手作業で仕分けすることも考え、フォークリフトが入れる幅にしています」
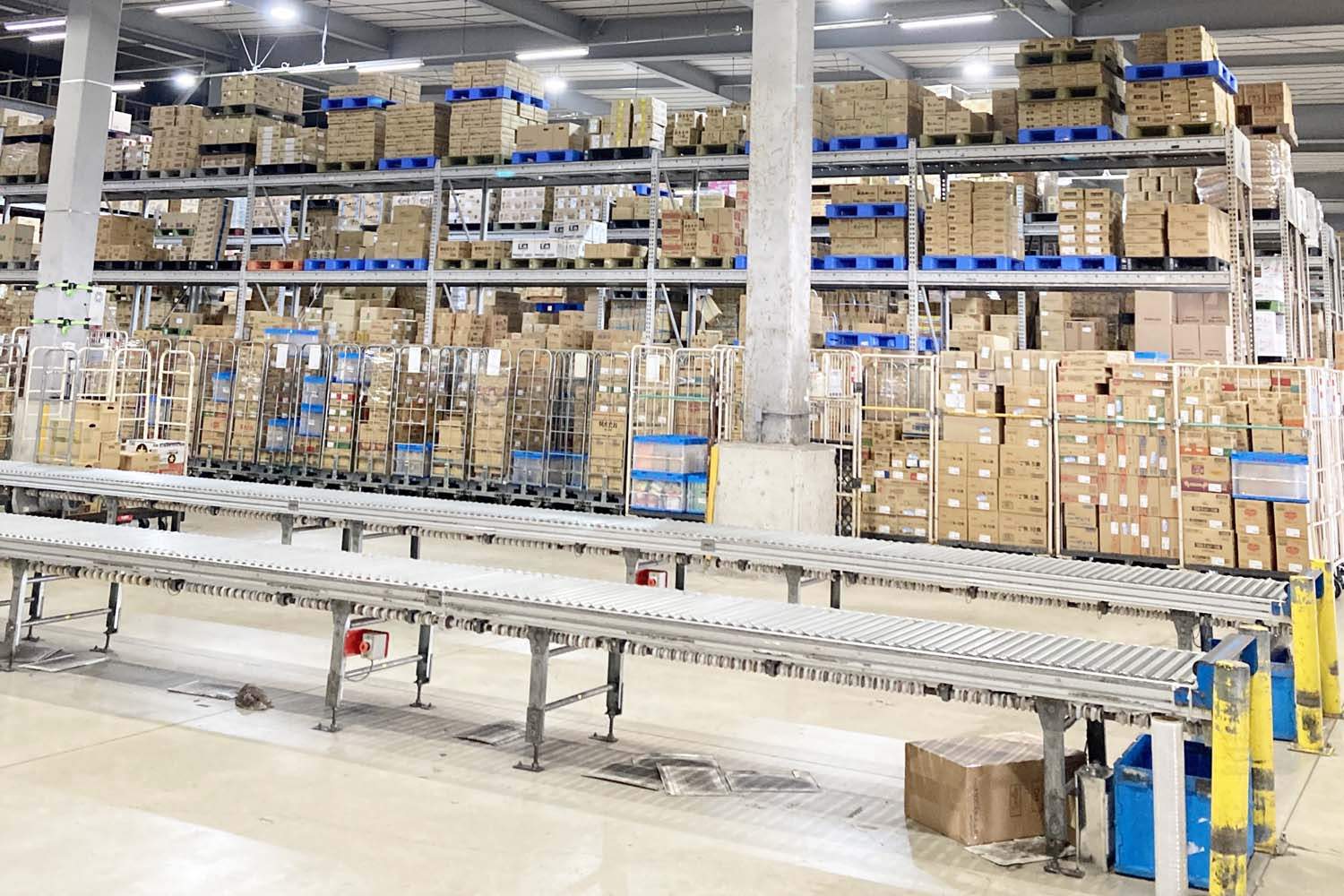
メーカーと密に連携し、いかに現場が使いやすいか、効率化できるかという視点に加え、トラブル時のリカバリーも織り込んでレイアウトやシステムをカスタマイズ。こうした工夫は、導入後のシステム変更をゼロにし、維持管理コストを抑えることにもつながっています。
1日も止めることができない物流ライン。毎日の作業が終わった夕方から深夜、3日間の工事を経て導入されたオートラベリングシステムにより、仕分け作業時間は4時間から2時間半に、1日10件以上発生していたラベルの貼り間違いはゼロに。大幅な効率化・時間短縮で、1日3~4時間があたりまえだった残業は大幅に改善し、週休2日(年間休日105日)も実現、スタッフの負担を大きく減らすことができました。
経営陣の同意と現場への浸透。そのハードルの乗り越え方
新たなシステムの導入には、経営層の同意が不可欠で、時に大きな壁となる場合もあります。石原さんはどのようにしてそれをクリアしたのでしょうか。
石原さん
「まずはシステムを導入・運用するコストとカットできる人件費の比較などを盛り込んだ資料を作り、役員会でプレゼンしました。効率化で残業が減り、作業が前倒しできて休みも取りやすくなれば定着率を上げられる点、現場が非熟練者でも作業できる環境になれば対応しなければならない問題も減り、その時間を新たな改善策を考えることに充てられる点もメリットとしてPRしました。
役員は普段は事務所にいることがほとんど。効率の悪さやスタッフの苦労をわかってもらうために、事務所から連れ出して現場を見てもらうことも大切です」
現場スタッフにとっても、慣れ親しんだやり方が大きく変わるため、浸透には工夫が必要でした。
ほぼ自動化されたシステムの中で、主にスタッフが担うのはレーンからの商品ピックアップとカゴ車(荷物運搬に使用される荷台を格子状の柵で囲んだ台車)への積込。商品ラベルに振られた識別用ナンバーをカゴ車のナンバーと照らし合わせて積み込むのですが、ピックアップが間に合わなくなってしまうのを避けるため、石原さんは同一商品が同一の配送先に連続して流れるのは2つまでに設定しました。
例えばAのケース商品12個を①~③の配送先に3個ずつ配送する場合、①~③に2個ずつ流し、その後また①から順に1個ずつ流れる仕組みです。
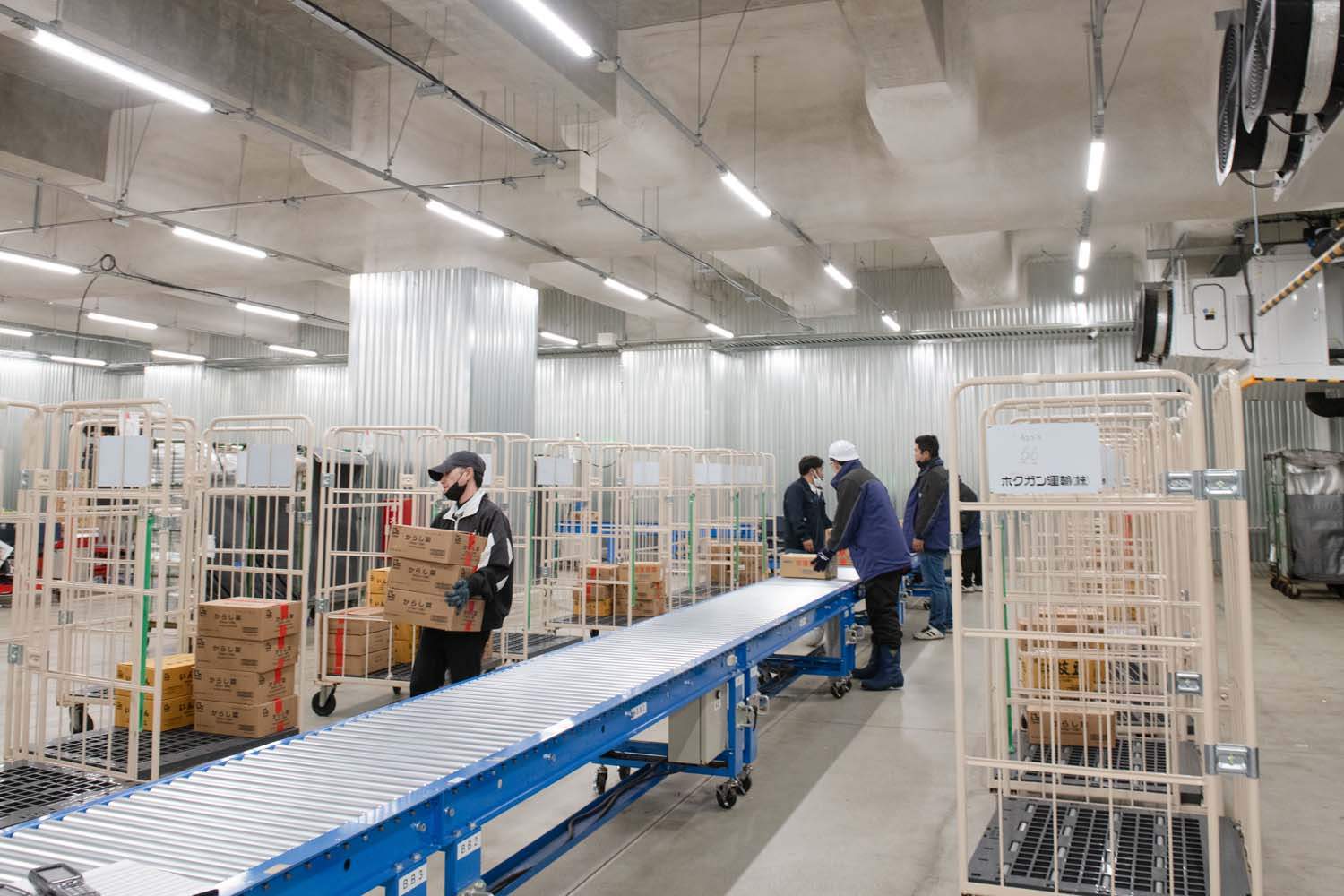
非常に理にかなった仕組みで、レクチャーも事前に行っていたものの、不慣れなために取り逃してしまうスタッフも多く、一時は現場が混乱する状況に。
「新しいシステムを入れるだけ入れて現場任せにしては、うまくいくはずがありません。2~3カ月間、スタッフが慣れるまで一人ずつ側についてサポートしました。普段から現場と苦労を分かち合うことができていれば、必ずついてきてくれます。メーカーさんの担当者も1ヶ月ほど滞在して、実際に使ってみなければわからない細かな調整や想定外の不具合調整に応じてくれたので、さらに使いやすいものになったと思います」
日々現場に立って課題や改善点を把握。国や県の補助金は大きな助けに
こうした様々な工夫により導入・構築されたシステムはしっかりと浸透し、非熟練者でも迷わず作業できる環境が整いました。万国共通の数字を使った仕分けは日本語に不慣れな方でも対応可能なため、外国籍スタッフの雇用も可能になり、現在6名が活躍しているのだそうです。
確実な仕分け作業が可能になったことで、たびたび発生してクレームや対応に追われていた納品間違いも起きなくなりました。また、予測しづらかった所要時間も、システム上に進捗のパーセンテージと仕分け残量が表示されることで明確に。スケジュールに遅れが出る場合でも「あと〇分で終了します」と連絡できるようになったことも相まって、取引先からの信頼と評価も高まっています。
2021年には、計約2万トンの保管が可能な冷凍倉庫・自動倉庫を備えた3階建の新本社が完成。オートラベリングシステムはもちろん、入荷と出荷を明確に区切る導線でモノと人の動きを最小限にする設計にも、石原さんの経験と知識が余すことなく反映されています。
さらには、国の補助事業である令和4年度沖縄物流デジタル技術活用推進事業にも採択。不鮮明な商品バーコード、縦のバーコードも読み取れるバーコードリーダーの導入も行ってさらに効率化を進めています。
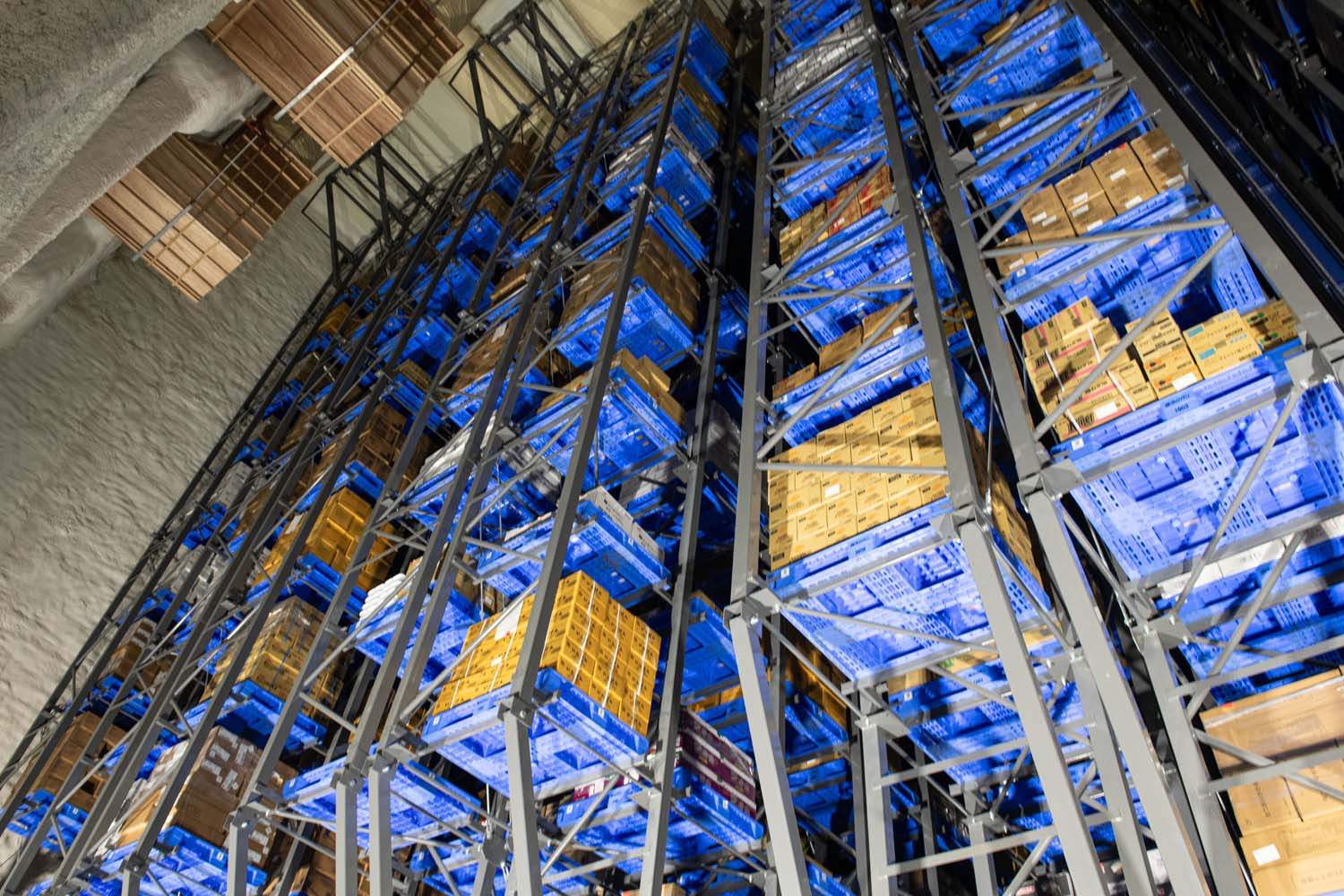
「物流業界では補助金の認知度が低いと感じています。私たちも県内で物流展示会が開催されたのをきっかけに産業支援センターとつながり、情報提供いただく中で初めて知りました。もっとたくさんの方にシステム導入や設備投資などへの補助金があることを知ってもらい、どんどん活用してもらいたいと思います」
仕分けの現場を文字通り作り変えた石原さんは、「自分が楽をしたいだけ」とこともなげに笑いながら、今も毎日現場に立っています。それは、現場が何に困っているのか、改善できる点はないかを把握するため。
「仕分けに関しては一通りの成果が出せたと思います。今後は2024年問題への対応のため、トラックの待機時間を短くするために何ができるかを考え、取り組んでいるところです」
日々私たちが手にする食料品や生活必需品。その物流を支える現場でも、DXは着実に進んでいます。